Blown Wing Aircraft
24-10-2019
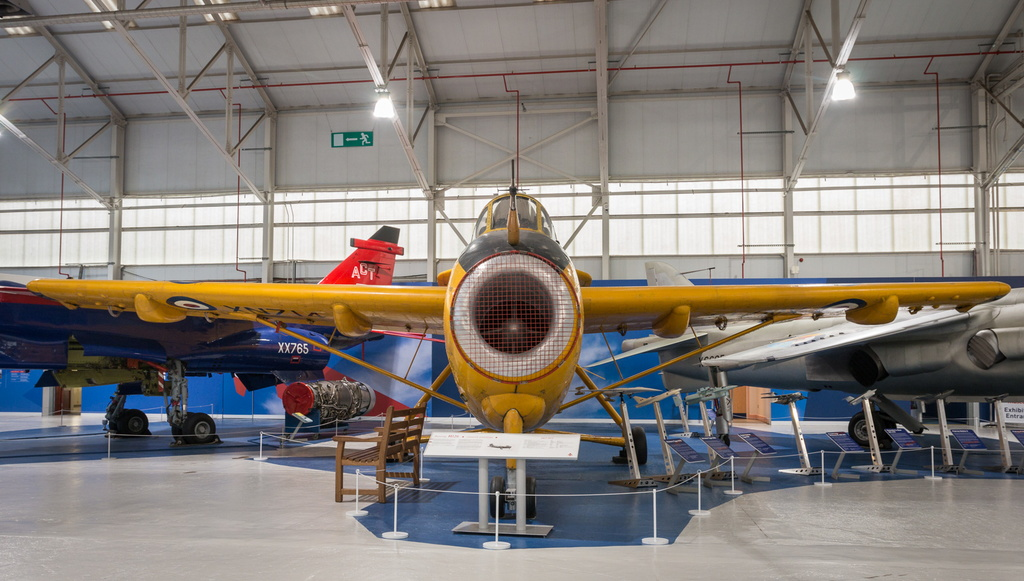
It was another of those conversations in the office. Tom has a background in aeronautical engineering, Jeff had found an article in a magazine and wanted to know more about the technology, especially in the use of small, powerful electric motors.
Blown wing is the principle of using the air generated by as a consequence of forward movement through it. This is re-directed down through nozzles over the rear edge of the wing, directing the flow downward, providing an increase to lift coefficient. In general, blown wing can improve the lift of a wing by two to three times. So why aren't they used everywhere?
Typically, blown flap is used for larger aircraft where increased lift is desired for STOL (short take off and landing). This leads to a natural advantage not only in enabling shorter runways, but greater stability at lower speeds; essential for larger aircraft.
The principle was proposed and patented in 1952 by the British National Gas Turbine Establishment (NGTE) and thereafter investigated by the NGTE and the Royal Aircraft Establishment. The concept was first tested at full-scale on the experimental Hunting H.126. It reduced the stall speed to only 32 mph (51 km/h), a number most aircraft could not and still can not match. The blown wing flap used a large percentage of the engine exhaust, rather than compressor bleed air, for blowing.
However, the major reason blown wing was not as widely effective is that the
airflow over the wing could only be "bent so much" before it stopped
following the wing profile, a condition known as flow separation.
Modern airliners use complex multi-part flaps for instance.
Large flaps tend to add considerable complexity, and take up room on the
outside of the wing, which makes them unsuitable for use on a fighter.
Dust and particulates can often clog inside the nozzles, requiring constant
maintenance. For this reason, they became increasingly out of favour during
the 70's after the war in Vietnam. There, a new method of
leading edge extensions were developed and incorporated into the
design of the F-16. This provided considerably more lift and negated the
expensive maintenance costs of blown wing design.
So, with little use of blown wing outside of all but the largest aircraft despite the maintenance requirements, is it an evolutionary dead end?
Not quite. Technology has caught up with the concept even more so, particularly in terms of low energy flight and reduced fuel consumption. Various designs too have been influenced from the concept of blown wing (see B2-Spirit) which are now being further refind and developed. NASA are experimenting with an electric, flying wing design.
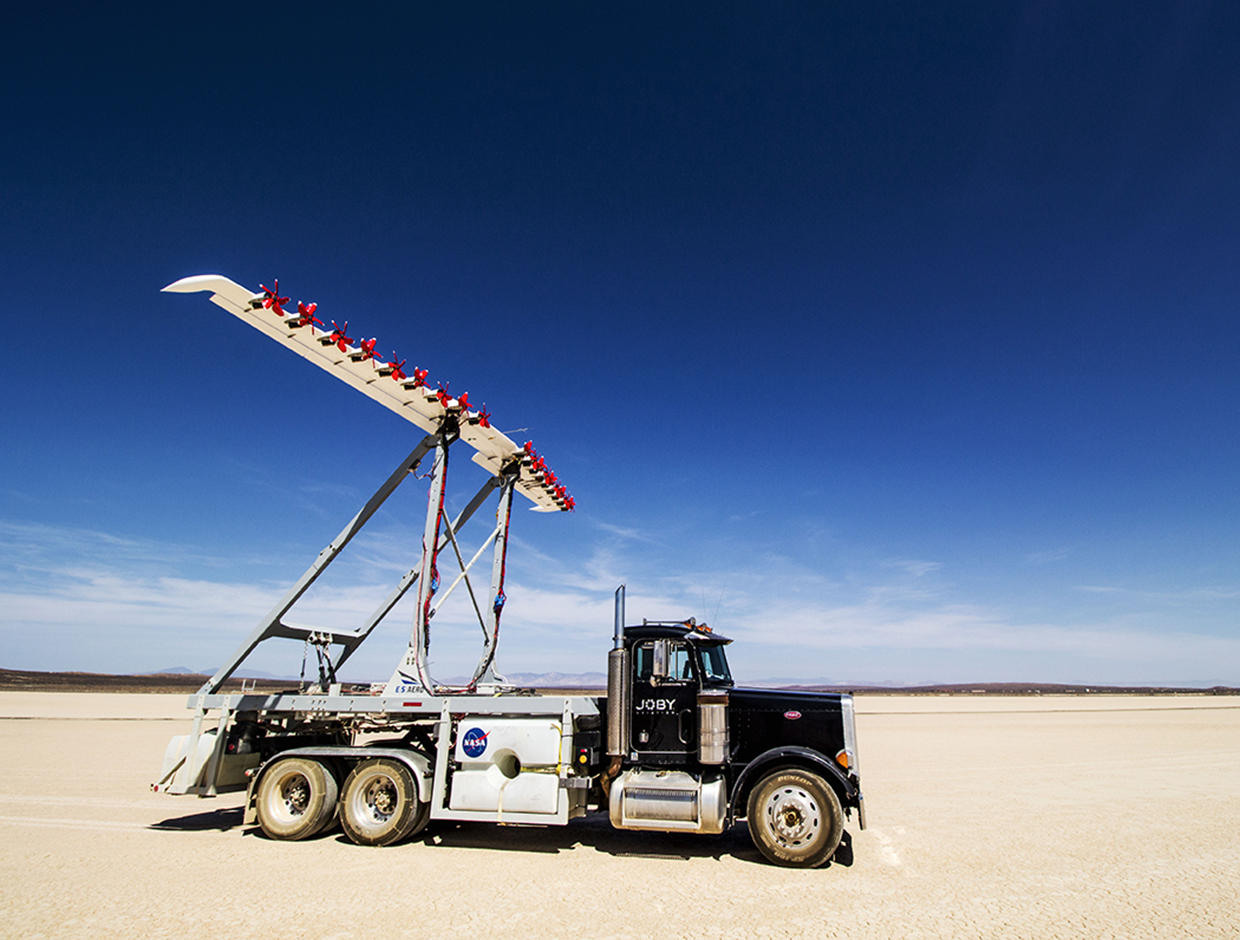
It would be more effective to distribute a large number of small propellers across the span of the wing, but for most of aviation history, that arrangement has been impractical. The problem is that the efficiency and specific power (the ratio of power output to weight) of combustion engines plummet as they’re scaled down. So using a large number of smaller engines results in a less efficient and heavier aircraft.
Electric motors don’t give up much efficiency or specific power as they’re scaled down. And they’re extremely simple—often having just one moving part—so they require very little maintenance. As a result, there is little disadvantage to using a large number of small electric motors, which can be placed at locations on the aircraft where a combustion engine would be impractically bulky or heavy, such as near the wingtips.
So why aren’t all aircraft battery powered? Because, of course, batteries aren’t yet up to the task. Even today’s best are very heavy for their energy content, which severely limits the range of electric aircraft.
So what were NASA's attempts to overcome this problem? The answer was LEAPtech (Leading Edge Asynchronous Propeller Technology) The blown wing principle, flying wing design coupled with requiring a lighter battery to power the increasingly efficient electric motors has shaken up designs of old.
LEAPTech Aerodynamic Simulation
The X-57 "Maxwell" was the result of this new technology, a test bed of cutting edge avionic and electronic design. To optimize performance, each motor can be operated independently at different speeds, decreasing reliance on fossil fuels, improving aircraft performance and ride quality, and reducing aircraft noise.
The propellers are mounted above the wing and will increase the air flow over the wing at lower speeds, increasing its lift. The increased lift allows it to operate on shorter runways, a stand out advantage of blown wing design. Because of this, the X-57 will be able to operate with 20% of the fuel cost than conventional aircraft. The range currently is 100 miles, though, supercapacitors made from graphene or materials like it will form an important part of our world in the near future.
Most of today’s airplanes and helicopters look very similar to models from many decades ago, but as this work demonstrates, that’s about to change. Thanks to the flexibility of electric propulsion, aviation is about to experience the greatest renaissance in design since the advent of the jet engine.