Bloodhound - A brief history of speed
18-12-2019
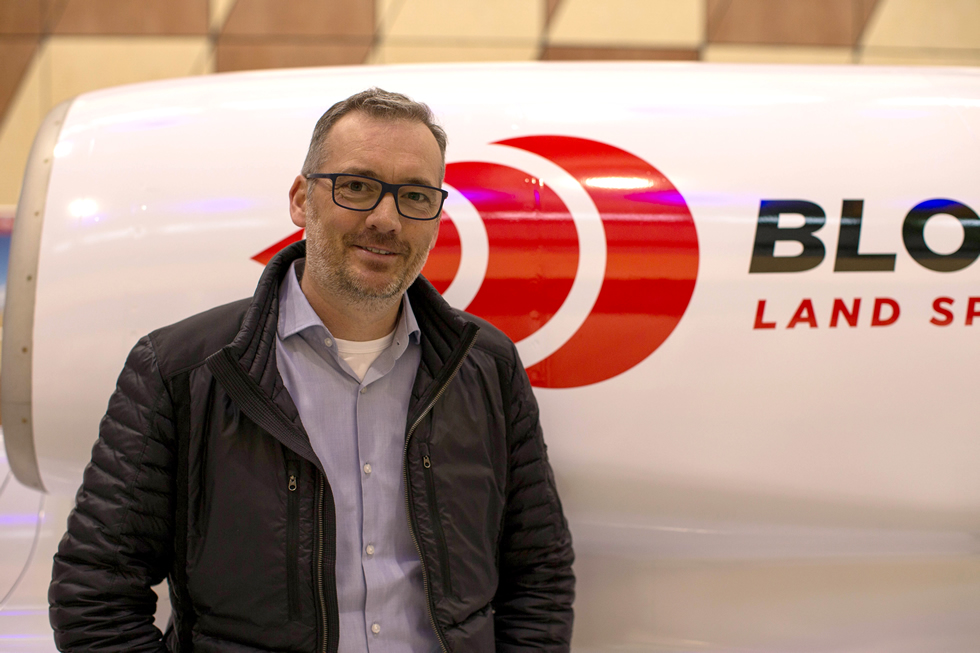
Bloodhound. A name almost anyone should be familiar with, even if all they could say was “the fast car?”
Named for a now retired RAF missile system that saw 40 years of service, the Bloodhound project was conceived by Richard Noble, the previous land speed record holder (and former paint salesman) who headed the Thrust2 and ThurstSSC projects.
After the run in ‘83 which earned him the Seagrave Trophy, the record was broken by RAF pilot Andy Green in ‘97, becoming the first person to break the sound barrier undertaken the ThrustSSC at 1221 km/h, the successor to Noble’s Thurst2.
The seeds were sown.
Development/Tech Specs
These higher speeds demand ever more power thanks to the immutable laws of physics; drag increases as the square of speed. A car that needs 100hp to reach 100mph would need 400hp to reach 200mph, or 900hp to reach 300mph. More power means bigger power plants, and Noble's Bloodhound SSC is a natural progression of this trend.
Noble and Green approached the UK government to see what could be done about supplying funding or equiptment. "We thought we'd earned the right to do this properly with the right technology," Noble told the UK's Director magazine. The Ministry of Defense agreed on the condition that Bloodhound rekindle an interest in STEM’s, and to hold a legacy that Apollo or Concorde created in the 1960s and 1970s. In return for inspiring a new generation of engineers, Bloodhound could have a prototype EJ200 jet engine, something you’d find on a Eurofighter Typhoon.
Whilst the EJ200 can output 20,000lbf (90kN) at full burn whilst weighing less than a ton, provides a considerable thrust to weight ratio compared to other power plants of its output and size. Initially developed for the Eurofighter project, the EJ200 has proven to be the most reliable military jet engine ever fielded by any air force and their uniquely low maintenance, replacement and bug-fixing requirements helped lower the Typhoon’s maintenance costs significantly.
Perfect then! Except not.
ThrustSSC used a pair F-4J Phantom’s General Electric J79-GE-17A to break the sound barrier. One EJ200 is roughly equivalent to one of the two engines of Bloodhound’s predecessor, albeit at half the weight. So where can the 30% increase come from?
The Bloodhound team decided that to save size and weight, a hybrid High-Test-Rocket (HTP) rocket would afford certain advantages over a pair of jets. Not only will it reduce the overall profile, but it would require only one air intake, resulting in lower drag. Whilst aircraft invariably operate with more than one jet, it would require designing variable geometry intakes. This adds weight, cost, and complexity. Additionally, a rocket provides far more thrust-to-weight ratio than a traditional turbofan and allows for rapid acceleration, with the final projected speed of 0-1000 MPH being achieved in just 49 seconds.
Development began in 2008 and took roughly 10 years to produce the working vehicle we see today. The College of Engineering at Swansea University were heavily involved in the aerodynamic design. Computational Fluid Dynamics (CFD) was to provide an understanding of the characteristics of the proposed shape, predicting drag forces, pitch and yaw stability and how heat would affect and warp the body.
The front section, including the cockpit and engine's air intake, is a carbon fiber monocoque, similar to a high performance race car (and some high end road cars). The rear encloses both engines and their ancillaries in a chassis made from machined aluminum, steel, and titanium. The design of the cockpit creates a shockwave just ahead of the EJ200’s air intake that pre compresses the air entering the jet, boosting engine power by a further 10%.
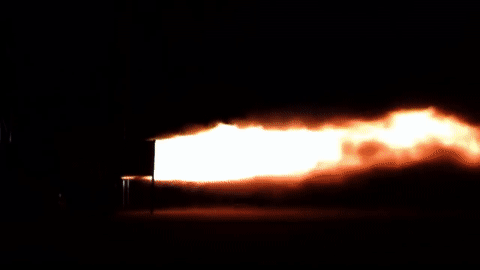
Bloodhound Project successfully tested its unique hybrid rocket system, for first time
Its wheels are solid disks of aluminum, each weighing more than 200lbs. They are lighter and stronger than conventional wheels, with no possibility of a puncture. They are connected to the car by springs and dampers tuned to soak up the bumps—as best as possible—at 1.4 times the speed of sound.
Pumping the fuel into the rocket was to be driven by a 12-cylinder V8 Jaguar engine, though this is to be undertaken by an electric engine when by the time the hybrid rocket is installed next year. From a safety point of view, you don’t want to mix hydrogen peroxide with anything organic like oil. At the time when it was designed the technology didn’t really exist for a capable enough electric engine, but with the advent and advancement of electric cars in the last few years, an electric engine will certainly be fit for purpose.
Crisis
However, in late 2018 the BloodhoundSSC company entered administration. Andrew Sheridan, a joint administrator at FRP Advisory, said: “Bloodhound is a truly groundbreaking project. Entering into administration provides some breathing space to identify an investor who will bring the guaranteed funding, impetus and expertise required to drive the project forward.”
Soon after, in December, a Yorkshire businessman Ian Warhurst stepped in to secure the funding for Bloodhound for an undisclosed sum. “Ian has a strong background in managing highly successful businesses in the automotive engineering sector and he will bring considerable expertise to bear in taking the project forward,” said Sheridan of the project’s new custodian.
Which is fortunate, as the majority of the work had been completed and testing was planned in 2019. To find a backer so soon from October demonstrates the passion this project exudes, and its importance to bolster STEM subjects. It just needed the right person to see it.
“I thought I’d retired” said Ian. “I’ve been running my own business for the last 16 years (Turbocharger specialist Melett). I sold the business in 2017 and retired officially at the end of November. I had no plans to do anything other than take it easy and enjoy life.”
“I’d been following the Thrust SSC project back in the 90s and thought it was fantastic, and I’d been following Bloodhound. I became a member of the 1k club (the supporters club) in 2009. My son came here to the NEC to do a STEM rocket car challenge and he thought it was great, so I knew the project was doing a really good job inspiring new engineers.”
“I got involved in this because of the STEM. Britain needs more engineers. What’s been fantastic about this project is the inspiration it gives to people to get into engineering. Because it’s been going 10 years there are people who were inspired back in 2010 who are now engineers.”
According to Ian, the project was very nearly ‘cut‘.
“The MOD were banging the door down trying to get in to take their stuff out, and the administrators couldn’t get it out because it was very deep inside the car so they came to the conclusion that the only way of getting this thing out was getting an angle grinder and cutting the car in half.”
“I knew when I left that building if I hadn’t done a deal the next man in that building was the man with the angle grinder coming to break it all up, so I did a deal. On Wednesday we were talking to each other; on Thursday I was confirming the contract and on Friday morning I signed up, job done. I then owned this massive long car!”
With the project saved and in passionate hands, development was able to continue, and most of the original team were brought back on board. Contracts were renewed, the logo and livery rebranded, BloodhoundSSC was renamed BloodhoundLSR and the team found a new home in Berkeley Green UTC in Gloucestershire. All of this has happened in just 12 weeks.
And by an amazing coincidence, they have moved close to us! The Gloucestershire Science and Technology Park is in the heart of the technical college.
With it accompanies an engineering school, and multiple onsite businesses that provide engineering expertise and support, with the Bloodhound set and centre stage for the next batch of apprentice engineers to fawn over and be inspired by. The prospect of collaboration for students and Bloodhound is not only an impressive accolade to have on one’s CV, but provides unparalleled and a retrospectively historic experience.
As the largest STEM programme currently in the UK, this is the opportunity any engineer would dream of.
Current Trials
In October, the project finally got underway and began the 5,500 mile trip to South Africa, bound for the 12 mile long Hakskeen Pan desert track with high speed testing which began at the end of that month.
The EJ200 engine was of particular concern being shipped out of the country, which had to wait until all the paperwork was in place (borrowing a state-of-the-art military jet engine is, quite rightly, a non-trivial process).
The first trial was toward late October, with the three ‘profile’ speed runs increasing in 100mph increments. 100, 200 and then 334mph accelerating from 0 - 334mph in 17 seconds. The car must be tested in stages, as going straight for the LSR would be running before one could walk in a manner of speaking.
Then on the 1st of November, Bloodhound reached 461mph. However, this was to test the functionality of it’s carbon-fibre air brakes and if they conform to theoretical computer simulations.
"In any computer model, there are some big assumptions - assumptions, for example, about the dust entrainment behind the vehicle, or exactly how the wheels interact with the ground.” stressed Dr Ben Evans, one of the aerodynamicists on the project. "It's important therefore that we get a feel for whether those assumptions are sensible. So far in these trials, it's looking good.
On November 19th, Bloodhound reached 1010kmh (628mph) after confidence in the prior warm up tests indicated good viability in the car. Andy Green commented by saying “the car is worse to drive than I had hoped, as the ever increasing speed makes handling the Bloodhound more challenging. This isn’t due to the nature of the car, however. It’s to do with the lateral wheel grip on the desert. At low speeds it’s like driving from snow onto ice – we were expecting that would happen at around 300, 350, 400mph but then at 500-600mph the aero load would build back up.”
Now the Bloodhound has been put through its paces, testing will wrap up until next year, by which time the HTP rocket will be installed. This will allow Bloodhound to reach speeds of 1000mph, far exceeding that of its predecessors, though 800mph is being settled on as a target for now. Nammo (the HTP builders) needs performance data acquired during the trials to design the nozzle for maximum efficiency. But they’re also looking at the practicalities of being out in the desert: how much refrigeration the rocket oxidiser is going to need and how to keep the fuel free from contamination.
Goal
Goal The team hopes to add this to the British escutcheon, a pioneer to bring STEM’s into the forefront of more schools and inspire the next generation. To catalyze the next generation of young people into STEMS is and always was the projects primary goal; if the land speed record is again beaten, no matter how much by, then the Bloodhound is undoubtedly fit for purpose. The technology behind and the dedication by the engineering team involved in Bloodhound will be a testament to its success. A success Richard Noble, Andy Green and countless have no doubts they can achieve.